In the realm of garment manufacturing, the choice of needle brand plays a pivotal role in ensuring efficiency, precision, and the quality of the end product. Sewing factories meticulously select needle brands that align with their specific production needs, considering factors such as fabric type, thread count, and desired stitch quality.
Among the leading needle brands used in sewing factories worldwide are:
- Groz-Beckert
- Schmetz
- Organ
- SINGER
- DBx
These brands have established a reputation for producing high-quality needles renowned for their durability, reliability, and ability to produce precise and consistent stitches. Moreover, they offer a wide range of needle types and sizes, catering to the diverse requirements of different fabrics and sewing techniques.
Choosing the appropriate needle brand is essential for optimizing sewing factory operations. The right needle ensures efficient fabric penetration, minimizes skipped stitches, and reduces thread breakage, ultimately leading to increased productivity and reduced downtime.
Needle Brands Used in Sewing Factories
The selection of needle brands in sewing factories is a critical aspect that influences the efficiency, quality, and productivity of garment manufacturing. Key factors to consider when choosing a needle brand include:
- Quality: High-quality needles ensure precise stitching, minimize skipped stitches, and reduce thread breakage.
- Durability: Durable needles withstand the rigors of continuous use, reducing downtime and maintenance costs.
- Variety: A wide range of needle types and sizes allows for optimal performance with different fabrics and sewing techniques.
- Availability: Consistent access to the chosen needle brand is crucial for uninterrupted production.
- Cost: The cost of needles should be balanced against their quality, durability, and impact on overall productivity.
- Reputation: Established needle brands with a proven track record inspire confidence and reliability.
Understanding these key aspects empowers sewing factories to make informed decisions when selecting needle brands. By choosing the right needles, factories can optimize their operations, enhance product quality, and increase profitability.
1. Quality
In the context of “what needle brand is used in sewing factories”, the quality of the needle is paramount. High-quality needles are essential for ensuring precise stitching, minimizing skipped stitches, and reducing thread breakage. This, in turn, leads to increased productivity, reduced downtime, and improved product quality.
- Precise Stitching: High-quality needles have sharp points that penetrate the fabric cleanly, creating precise and even stitches. This is especially important for delicate fabrics and intricate designs.
- Minimized Skipped Stitches: Skipped stitches can occur when the needle is blunt or damaged, causing the thread to loop or break. High-quality needles maintain their sharpness over time, reducing the likelihood of skipped stitches and ensuring a smooth, professional finish.
- Reduced Thread Breakage: Cheap or low-quality needles can have burrs or imperfections that can snag and break the thread. High-quality needles are smooth and polished, minimizing friction and reducing the risk of thread breakage.
Overall, the use of high-quality needles in sewing factories is directly linked to improved efficiency, reduced production costs, and enhanced product quality. By investing in high-quality needles, factories can optimize their operations and deliver superior garments to their customers.
2. Durability
In the context of “what needle brand is used in sewing factories”, durability is a crucial factor to consider. Durable needles withstand the rigors of continuous use, reducing downtime and maintenance costs, which are essential for efficient and profitable garment manufacturing.
- Reduced Downtime: Durable needles maintain their sharpness and integrity over extended periods, minimizing the need for frequent needle changes. This reduces downtime and keeps sewing machines running smoothly, maximizing productivity.
- Lower Maintenance Costs: Durable needles are less prone to breakage and bending, reducing the need for frequent maintenance and repairs. This saves factories time and money on maintenance costs, allowing them to allocate resources more effectively.
- Increased Productivity: Durable needles enable sewing machines to operate at optimal efficiency, minimizing interruptions and production delays. This leads to increased productivity and allows factories to meet production targets more effectively.
- Enhanced Product Quality: Durable needles contribute to improved product quality by producing consistent and precise stitches. This is especially important for garments that require intricate stitching or delicate fabrics.
Overall, the use of durable needles in sewing factories is directly linked to reduced operating costs, increased productivity, and enhanced product quality. By investing in durable needles, factories can optimize their operations and deliver superior garments to their customers.
3. Variety
In the context of “what needle brand is used in sewing factories”, variety is a key aspect to consider. A wide range of needle types and sizes allows sewing factories to select the optimal needle for each specific fabric and sewing technique, ensuring the highest quality and efficiency in garment production.
Different fabrics have unique characteristics that require specific needle types to achieve optimal performance. For instance, delicate fabrics such as silk or chiffon require fine needles with sharp points to prevent snagging or tearing. Conversely, heavy-duty fabrics like denim or canvas necessitate stronger needles with larger eyes to accommodate thicker threads.
Similarly, different sewing techniques demand different needle sizes. Topstitching, for example, which involves dekoratif stitching on the surface of the fabric, requires a larger needle to create a prominent effect. Conversely, intricate embroidery or applique work may require smaller needles to achieve precision and detail.
By offering a wide range of needle types and sizes, needle brands cater to the diverse needs of sewing factories. This allows factories to optimize their production processes, minimize fabric damage, and achieve the highest quality standards in their garments.
In conclusion, the variety of needle types and sizes is an essential component of “what needle brand is used in sewing factories”. It empowers factories to select the optimal needle for each specific fabric and sewing technique, ensuring efficient and high-quality garment production.
4. Availability
In the context of “what needle brand is used in sewing factories”, consistent access to the chosen needle brand is paramount for maintaining uninterrupted production and maximizing efficiency. Sewing factories rely on a steady supply of needles to meet their production targets and ensure timely delivery of garments to their customers.
- Reduced Downtime: Consistent access to the chosen needle brand minimizes downtime caused by needle shortages or delays in needle delivery. Factories can maintain a smooth workflow without interruptions, ensuring optimal production capacity.
- Improved Planning: When sewing factories have consistent access to their preferred needle brand, they can plan their production schedules more effectively. They can accurately estimate needle consumption and place orders in advance, reducing the risk of unexpected shortages.
- Quality Control: Using a consistent needle brand allows factories to maintain standardized quality throughout their production processes. Needles from the same brand are manufactured to precise specifications, ensuring consistent stitch quality and minimizing the risk of fabric damage or skipped stitches.
- Cost Optimization: Consistent access to the chosen needle brand enables factories to negotiate favorable pricing and secure bulk discounts. This can lead to significant cost savings over time, contributing to the overall profitability of the factory.
Overall, consistent access to the chosen needle brand is essential for sewing factories to maintain uninterrupted production, optimize efficiency, and deliver high-quality garments to their customers. By establishing reliable partnerships with needle suppliers and implementing effective inventory management systems, sewing factories can ensure the availability of the needles they need, when they need them.
5. Cost
The cost of needles is an important factor for sewing factories to consider when selecting a needle brand. While it may be tempting to opt for the cheapest needles available, it is crucial to balance cost with quality, durability, and the overall impact on productivity.
High-quality needles may come with a higher upfront cost, but they offer several advantages that can lead to significant savings in the long run. Durable needles withstand the rigors of continuous use, reducing the need for frequent replacements and minimizing downtime. This increased durability also contributes to fewer skipped stitches and thread breakage, resulting in less wasted fabric and thread.
Moreover, the use of high-quality needles can improve sewing efficiency. Precise and sharp needles penetrate the fabric cleanly, allowing sewing machines to operate smoothly and at optimal speeds. This reduces cycle time and increases productivity, leading to higher output and reduced labor costs.
In summary, while cost is an important consideration, sewing factories should not solely focus on the initial purchase price of needles. By considering the broader implications of needle quality, durability, and impact on productivity, factories can make informed decisions that optimize their overall efficiency and profitability.
6. Reputation
Within the context of “what needle brand is used in sewing factories”, reputation plays a significant role in shaping the choices made by these factories. Established needle brands that have built a strong track record of quality, durability, and reliability inspire confidence among manufacturers.
- Consistent Quality: Reputable needle brands adhere to stringent quality standards, ensuring that their needles consistently meet the required specifications. This consistency gives factories peace of mind, knowing that they can rely on the needles to perform as expected, reducing the risk of production disruptions.
- Proven Durability: Established needle brands have a proven track record of producing needles that withstand the rigors of industrial sewing environments. Their needles are designed to maintain their sharpness and integrity over extended periods, minimizing the need for frequent replacements and reducing downtime.
- Reliable Performance: Sewing factories rely on needles to deliver consistent and reliable performance. Reputable needle brands have earned a reputation for producing needles that produce precise stitches, minimize skipped stitches, and reduce thread breakage. This reliability is crucial for maintaining high productivity and minimizing fabric waste.
- Established Partnerships: Many reputable needle brands have long-standing partnerships with sewing factories, fostering close relationships built on trust and mutual respect. These partnerships ensure that factories have access to the latest needle technologies and receive ongoing support, contributing to the overall efficiency and success of their operations.
In summary, the reputation of needle brands is closely intertwined with the decision-making process in sewing factories. By choosing established needle brands with a proven track record, factories can inspire confidence and reliability, ensuring the highest quality and efficiency in their garment production.
Tips and Benefits of Choosing the Right Needle Brand for Sewing Factories
Selecting the optimal needle brand is crucial for sewing factories seeking efficiency, quality, and profitability. Here are some guidelines and tips to assist in making informed decisions:
- Assess Fabric and Thread: Determine the type of fabric and thread being used, as different materials require specific needle types and sizes for optimal performance.
- Consider Sewing Technique: The intended sewing technique, such as topstitching, embroidery, or applique, influences the choice of needle point style and size.
- Evaluate Needle Quality: Opt for high-quality needles made from durable materials to ensure longevity and minimize skipped stitches and thread breakage.
- Ensure Consistent Supply: Establish a reliable partnership with a needle supplier to guarantee consistent access to the chosen needle brand, avoiding production disruptions.
- Consider Cost-Effectiveness: While cost is a factor, prioritize needles that offer a balance of quality, durability, and impact on overall productivity.
- Seek Expert Advice: Consult with industry experts or experienced sewing professionals to gain insights and recommendations on needle selection.
Tip 1: Prioritize Quality: Investing in high-quality needles reduces downtime, minimizes fabric waste, and enhances stitch quality, leading to increased productivity and profitability.
Tip 2: Match Needle to Fabric: Using the appropriate needle type and size for the specific fabric prevents fabric damage, skipped stitches, and ensures optimal seam strength.
Tip 3: Maintain Sharp Needles: Regularly replace or sharpen needles to maintain their precision and prevent fabric snags, thread breakage, and uneven stitching.
Tip 4: Store Needles Properly: Store needles in a dry and organized manner to prevent rust and damage, ensuring their longevity and performance.
Tip 5: Train Operators: Educate sewing machine operators on proper needle handling and maintenance practices to optimize needle life and minimize production issues.
Summary of key takeaways or benefits:
- Selecting the right needle brand enhances production efficiency, reduces costs, and improves product quality.
- Matching needles to specific fabrics and sewing techniques optimizes performance and minimizes fabric damage.
- Investing in high-quality needles leads to increased productivity and profitability in the long run.
- Proper needle care and maintenance practices extend needle life and ensure consistent performance.
- Educating sewing machine operators on needle handling contributes to overall production efficiency.
Transition to the article’s conclusion:
By following these guidelines and tips, sewing factories can make informed decisions when selecting needle brands. This empowers them to optimize their production processes, enhance product quality, and achieve greater efficiency and profitability.
Frequently Asked Questions about Needle Brands in Sewing Factories
This section addresses frequently asked questions (FAQs) regarding needle brands used in sewing factories, providing informative answers to common concerns and misconceptions.
Question 1: What factors should be considered when selecting a needle brand for a sewing factory?
Answer: Key factors include needle quality, durability, variety of types and sizes, consistent availability, cost-effectiveness, and the reputation of the needle brand.
Question 2: How does needle quality impact sewing factory operations?
Answer: High-quality needles minimize skipped stitches, reduce thread breakage, and ensure precise stitching, leading to increased productivity and reduced downtime.
Question 3: Why is needle durability important for sewing factories?
Answer: Durable needles withstand the rigors of continuous use, minimizing downtime and maintenance costs while maintaining consistent stitch quality.
Question 4: How does the variety of needle types and sizes benefit sewing factories?
Answer: A wide range of needle types and sizes allows factories to optimize performance for different fabrics and sewing techniques, ensuring the highest quality and efficiency.
Question 5: Why is consistent access to the chosen needle brand crucial for sewing factories?
Answer: Consistent access minimizes downtime, improves planning, ensures quality control, and enables cost optimization through favorable pricing and bulk discounts.
Question 6: How can sewing factories make informed decisions when selecting needle brands?
Answer: Factories should assess fabric and thread types, consider sewing techniques, evaluate needle quality, ensure consistent supply, consider cost-effectiveness, and seek expert advice.
Summary of key takeaways or final thought:
Understanding the importance of needle brand selection and considering the factors discussed in these FAQs empowers sewing factories to make informed decisions. By choosing the right needle brands, factories can optimize their production processes, enhance product quality, and achieve greater efficiency and profitability.
Transition to the next article section:
The following section will delve into specific needle brands commonly used in sewing factories, exploring their unique features and benefits.
Conclusion
The choice of needle brand is a critical aspect of sewing factory operations, influencing efficiency, quality, and profitability. By considering factors such as needle quality, durability, variety, availability, cost, and reputation, factories can make informed decisions that optimize their production processes.
Investing in high-quality needles minimizes downtime, reduces fabric waste, and enhances stitch quality, leading to increased productivity and profitability. Matching needles to specific fabrics and sewing techniques ensures optimal performance and minimizes fabric damage. Proper needle care and maintenance practices extend needle life and ensure consistent performance.
Educating sewing machine operators on needle handling contributes to overall production efficiency. By following these guidelines, sewing factories empower themselves to make informed needle brand selections, ultimately enhancing their competitiveness in the global market.
Youtube Video:
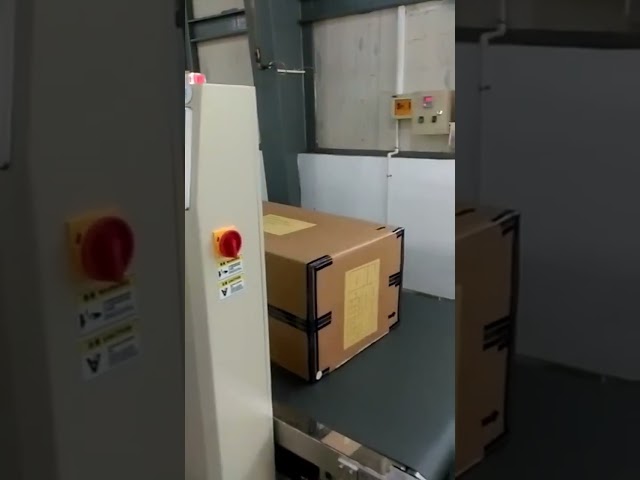